By choosing eco-friendly construction materials for building your dream house, you are not just doing your bit to conserve the environment but also saving on your overall construction costs. Among the innovative construction materials used across the world, autoclaved aerated concrete blocks (AAC blocks or bricks) are considered superior to other conventional materials like burnt clay bricks that cause environmental hazards. The benefits of AAC blocks as an affordable and sustainable alternative to traditional building materials are being widely recognised in India. In this article, we explain AAC blocks and their advantages and disadvantages in house construction.
AAC block full form
AAC blocks are also known as autoclaved aerated concrete blocks, which are one of the environment friendly and lightweight construction materials.
What are AAC blocks?
AAC blocks are a precast, foam concrete, sustainable construction material made from aggregates of quartz sand, calcined gypsum, lime, portland cement, water and aluminium powder. After mixing and moulding, the concrete is autoclaved under heat and pressure and it thus gains its distinctive properties. AAC bricks are in high demand, owing to their high strength, load-bearing and thermal insulation properties.
AAC block is used as a construction material for interior and exterior structures. The blocks may be coated with a stucco finish or with siding materials like veneer brick or vinyl siding.
AAC block: Features
Colour | Greyish-white |
Lightweight | 50% lighter than red bricks |
Fire resistance | Between two and six hours, based on the thickness |
Energy efficiency | 25% reduction in air-conditioning costs |
Thermal efficiency | Three times higher than clay bricks |
Water absorption | About 10% of its weight |
Sound insulation | 42 dB (approximately) |
Affordable cost | Nearly one-third of the cost of regular bricks |
Also read all about 3D house in India
AAC block price: AAC blocks sizes and prices
Manufacturers of autoclaved aerated concrete produce AAC blocks ranging in varied sizes and strengths. The AAC block price for rectangular AAC bricks having size (length X height X weight) of 600mm x 200mm x 250mm can range between Rs 2,000 and Rs 3,500 per cubic meter. The AAC blocks sizes and prices differ, depending on the manufacturer.
Also read: Bamboo house design and construction ideas for sustainable living
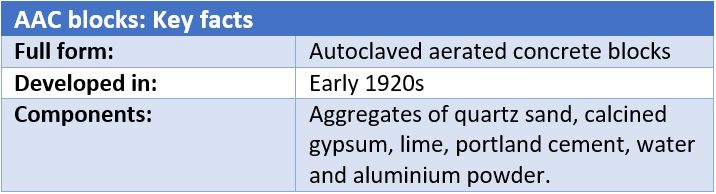
AAC blocks are available in different sizes, which include:
- 600mm x 200mm x 50 mm
- 600mm x 200mm x 75 mm
- 600mm x 200mm x 100 mm
- 600mm x 200mm x 150 mm
- 600mm x 200mm x 200 mm
- 600mm x 200mm x 230 mm
- 600mm x 200mm x 250 mm
- 600mm x 200mm x 300 mm
Also read all about the building code guidelines for residential buildings
AAC blocks arrangement
The material is available as AAC blocks and panels. These blocks are arranged in stacks in the same manner as in conventional masonry. However, a thin-layered mortar, and panels are vertically arranged. For structural purpose, grouted, reinforced cells and beams included within the section of the wall. The blocks can be arranged manually with hands. However, the placement of the AAC panels need the support of equipment like crane due to their large size.
AAC blocks shapes
- Lintel blocks, which are also referred to as U-shaped bond beam are available in thickness of 8, 10, and 12 inches.
- Tongue-and-groove AAC blocks or slabs are available in large sizes. These blocks are linked to adjacent units without the use of mortar at the vertical edges.
- Cored blocks are used in building vertical reinforced grout cells.
AAC blocks advantages and disadvantages
What are the advantages of AAC blocks?
In today’s times when the world is realising the importance of environmental conservation, the construction sector has also witnessed technological advancements, including the use of innovative and sustainable construction materials. Here are some of the advantages of AAC bricks:
Better workability and faster construction
AAC blocks are about 50% lighter and 10 times larger than traditional bricks. This unique property facilitates easy installation and gives the desired flexibility that makes adjustments, cutting, shaping, etc., quite easy. AAC blocks have fewer joints and consistent dimensions, thereby, ensuring ease of laying and making the construction process faster. Lastly, the lightweight blocks are easy to transport, which helps to save on the overall logistics and shipping costs, as compared to the costs involved in the transportation of traditional bricks.
Earthquake-resistant
Generally, buildings are designed to handle vertical forces, such as self-weight and gravity. However, there are also horizontal forces, such as those caused by earthquakes. The AAC blocks gain a high level of strength during the manufacturing process, giving durability to the finished structure. Thus, structures made with AAC bricks are capable of handling higher seismic loads, compared to structures with conventional bricks.
See also: How can home owners ensure earthquake-resistant homes?
Thermal insulation and energy-efficiency
The material contains small air pockets and hydrogen is used to foam the concrete, thus, giving it an excellent heat insulation property that allows temperatures to be warm in winters and cool in summers. Therefore, it can significantly lower your air-conditioning costs by about 25%. AAC blocks are energy-efficient across their lifecycle, as their production involves less energy consumption.
Fire-resistant
The AAC block material is non-combustible and provides fire resistance of up to six hours, depending on the block thickness and up to 1,200 degrees Celsius, compared to other building materials. Thus, it also has importance from a fire safety point of view.
Sustainable and affordable
AAC blocks are made from natural and non-toxic raw materials and their manufacturing process generates minimum waste. Some of the waste or offcuts generated can be recycled or used in aggregates. As it is made from non-biodegradable materials, it makes the building durable and stable, preventing rot or mold. Furthermore, being lightweight, energy-efficient and easy to install, AAC blocks also minimise labour costs.
High compressive strength
The average compressive strength of the AAC block is 3 to 5 N/mm2. Thus, it is much stronger and better than bricks of the same density.
Pest-resistant
AAC blocks are prepared from inorganic materials, which help in protecting the structure from pests such as termites, rodents, etc.
Soundproof
The lightweight and porous structure of AAC blocks enables high sound reduction. For this reason, the AAC block material is widely used in the construction of studios, hotels, hospitals, etc.
Moisture-proof
Moisture can severely damage a structure. The macro-pores inside AAC blocks ensure low absorption of water. Thus, they provide better moisture protection.
See also: A guide to waterproofing your home
When it comes to small-scale building projects, red bricks may still find their importance. However, for large-scale residential, commercial and infrastructure projects, AAC blocks provide greater benefits and play a significant role in controlling the environmental damage caused due to construction using outdated building materials.
AAC blocks disadvantages: Why is AAC block not used in foundation?
Although AAC blocks are widely used in masonry units of high-rise RCC (reinforced cement concrete) framed buildings, they can be expensive when used for small load-bearing structures. When using AAC blocks, it could be one of the disadvantages. Considering the high AAC block prices, buying a small number of blocks for such structures can cost more, as compared to ordering in bulk quantities for large projects. However, the material is lightweight and thus, contributes less to dead load and the requirement of structural steel can be minimised in RCC framed structures. Therefore, it can save on construction costs, when chosen for high-rise constructions.
Further, column foundations in RCC framed structures are designed for bearing the load of a building. In such structures, RCC foundations are arranged on which RCC columns are raised. Plinth beams are placed at the plinth level and AAC block masonry is raised on it. Thus, there is no need for AAC block masonry between the columns below the DPC level plinth beam. DPC or damp-proof course refers to material applied at the basement level, for restricting moisture flow through walls and floors.
Load-bearing is used for low-rise structures. The thickness of the walls and finding the right size of AAC blocks, are crucial aspects, when it comes to load-bearing walls. Moreover, the placement of these blocks requires expertise. It is important that the walls are designed by a qualified structural engineer.
See also: Mobile tower installation rules and regulations
AAC blocks installation
The installation of AAC blocks is similar to that of the conventional concrete masonry. The placement of AAC panels require the support of a crane. Based on the type of finish, the panels can be directly adhered or attached mechanically to the surface of AAC.
AAC blocks finishes
- AAC blocks are available in stucco-type finishes. The polymer-modified plasters seal against water entry. However, they allow moisture vapour for breathability.
- Masonry veneers can be adhered directly to the face of a wall. They can also be built as cavity walls. Like a manufactured stone, direct-applied veneers are usually lightweight.
- Conventional siding materials are mechanically connected to the face of a wall. Furring strips must be used in case of back ventilation of the siding material is needed.
AAC blocks: Where are they used?
AAC blocks are widely used in the construction of apartments and other types of residential properties, industrial and commercial buildings, such as hotels, offices, hospitals and schools. Owing to their excellent heat insulation capacity, AAC bricks find application in interior and exterior construction. They are ideal for high-rise structures.
See also: Everything you need to know about eco-friendly homes
AAC blocks vs red bricks
AAC blocks manufacturers are sought-after by construction companies in India, as this new-age building material scores over traditional bricks for numerous reasons.
Firstly, bricks are heavier and their use in building construction involves increased cost and wastage. Moreover, the rising price of kiln fuel can impact the overall cost. AAC blocks, on the other hand, are lightweight. The weight of AAC blocks is about 80% less than traditional red bricks and leads to a reduction in the use of cement and steel, thus, saving costs. Moreover, being environmentally friendly, AAC blocks ensure better durability and improved sound and heat insulation compared to bricks.
See also: All about GST on bricks and other building materials
AAC blocks vs CLC blocks: Which is better?
CLC (cellular lightweight concrete) blocks are produced from cellular lightweight concrete (CLC) or foam concrete. It is a lightweight concrete made by combining cement and flyash slurry with pre-formed foam. CLC blocks are comparatively cheaper than AAC blocks. However, in terms of compressive strength, AAC blocks are better than CLC blocks.
See also: All about a turnkey project
AAC blocks: Background and history
In the early 1920s, Dr Johan Axel Erikkson, along with Professor Henrik Kreuger, developed AAC blocks. After patenting the manufacturing process in 1924, AAC blocks were produced in full swing from 1929 in Sweden.
Earlier, alum shale, a naturally formed clay slate comprising pyrite, was used by scientists for the process. The carbon content in pyrite facilitated the combustion process and the release of gases. In 1972, the Swedish government highlighted the release of harmful radon emissions when alum shale underwent combustion. Owing to this, the material was banned. An alternative was required, which was a blend of lime, cement, aluminium powder, and calcined gypsum.
Presently, AAC blocks manufacturing on a wide scale as construction material, is done across countries like the United States of America, Russia, Germany and India. The popularity of AAC blocks is steadily growing in many countries in Asia, including India, owing to increasing demand for housing units and commercial spaces. However, the market for this construction material is still in its nascent stages in India.
See also: All about penthouse
FAQs
Why AAC blocks get cracks?
Haphazard arrangement of the AAC blocks, shift in the beam placement, shift in the skeletal movements, because of change in water content or change in temperature, are some of the common reasons for AAC blocks developing cracks.
Do AAC blocks require plastering?
AAC blocks are wire cut and they have a plain surface. Due to this reason, plastering for internal walls is not required. Thus, wall putty and painting can be directly done. However, external plastering will be required.
Are AAC blocks good or bad?
Autoclaved aerated concrete is an innovative building material. It has unique properties that make it better than traditional bricks while giving protection to a building structure in many ways. Moreover, it is environment-friendly and saves overall construction cost. Hence, it is considered a good alternative to regular building materials like red bricks.
How do you repair a cracked AAC block wall?
One can use crack filling mortar that is specially manufactured for filling cracks on AAC block walls and plasters.
How many bricks equal to one AAC block?
One AAC block of dimension 600 x 200 x 100 mm is equivalent to six bricks.
Got any questions or point of view on our article? We would love to hear from you. Write to our Editor-in-Chief Jhumur Ghosh at [email protected]
Harini is a content management professional with over 12 years of experience. She has contributed articles for various domains, including real estate, finance, health and travel insurance and e-governance. She has in-depth experience in writing well-researched articles on property trends, infrastructure, taxation, real estate projects and related topics. A Bachelor of Science with Honours in Physics, Harini prefers reading motivational books and keeping abreast of the latest developments in the real estate sector.
Email: [email protected]